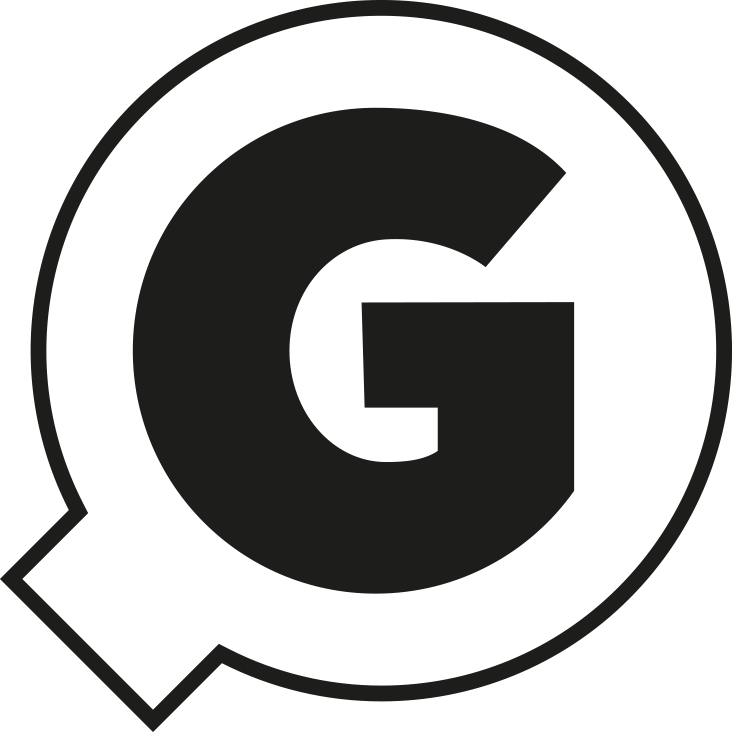
At GAPS, it is imperative to us that we can ensure our tooling solutions meet the highest industry standards for performance and reliability.
Our quality control process is comprehensive and requires that every order is thoroughly inspected and validated before it is delivered to our customers. We maintain an ISO 9001-2015 certification to guarantee that our products meet the highest quality standards. We are committed to delivering tooling solutions that offer the most competitive cost per piece for our customers. Our dedication to quality and continuous improvement is evident in every set of dies that we produce.
Inspection
At GAPS, we invest heavily in inspection and bespoke CNC production equipment to ensure the highest levels of quality and accuracy in our tooling solutions. Our inspection equipment includes a variety of optical, profile & surface analysis equipment, all of which are operated by highly skilled and experienced technicians. This allows us to measure and validate even the most complex geometries and tolerances and ensure that our products consistently meet the exacting standards of our customers.
One of the machines we use is the Mahrsurf XCR20 Profiling Machine coupled with a surface finish module. We have two of these machines, which are extremely precise and allow us to produce contour trace reports that can be provided with the tools to our customers.
Shadowgraphs are used in conjunction with custom-made laser-printed templates for visual inspections of thread forms.
Quality Policy
G.A.P.S. Services Ltd is fully committed to the manufacture, machining, servicing and supply of products which are fit for their intended purpose and which fully conform to our customer’s requirements.
To achieve this objective the Company has implemented an externally audited quality management system. It is under continuous review as G.A.P.S. Services Ltd strives for continuous improvement in quality.
Company policy is implemented, maintained and understood by all Employees and detailed in written procedures and works instructions and must be adhered to at all times. As such employees are responsible for the quality of their own work and are committed to participate in the operation of the quality management system.
The Managing Director has ultimate responsibility for the effective operation of the quality management system. He has delegated the responsibility for identifying and evaluating quality problems and for initiating, recommending and providing solutions to the Quality Manager and Leading Hands.
Graham Ayres
Managing Director
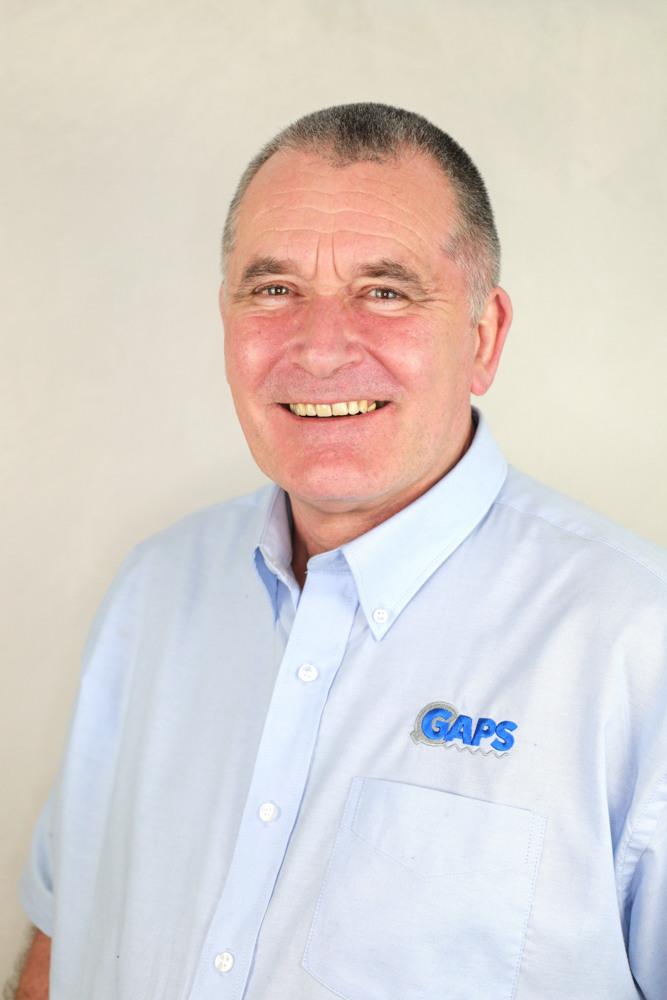